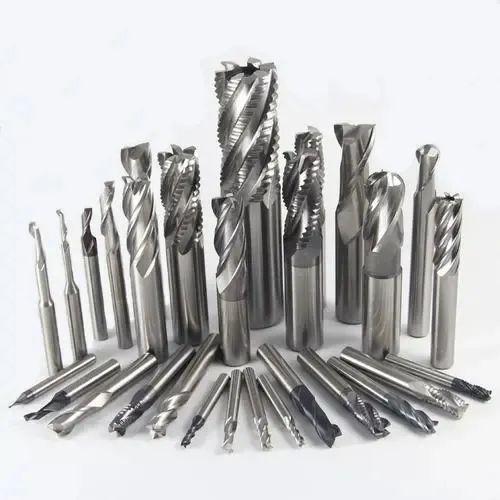
Modern cutting tool materials have experienced more than 100 years of development history from carbon tool steel to high-speed tool steel, cemented carbide, ceramic tool and superhard tool materials. In the second half of the 18th century, the original tool material was mainly carbon tool steel. Because at that time it was used as the hardest material that could be machined into cutting tools. However, due to its very low heat-resistant temperature (below 200°C), carbon tool steels have the disadvantage of being immediately and completely dull due to cutting heat when cutting at high speeds, and the cutting range is limited. Therefore, we are looking forward to tool materials that can be cut at high speeds. The material that emerges to reflect this expectation is high-speed steel.
High-speed steel, also known as front steel, was developed by American scientists in 1898. It is not so much that it contains less carbon than carbon tool steel, but that tungsten is added. Due to the role of hard tungsten carbide, its hardness is not reduced under high temperature conditions, and because it can be cut at a speed much higher than the cutting speed of carbon tool steel, it is named high-speed steel. From 1900~-1920, high-speed steel with vanadium and cobalt appeared, and its heat resistance was increased to 500~600 °C. The cutting speed of cutting steel reaches 30~40m/min, which is increased by nearly 6 times. Since then, with the serialization of its constituent elements, tungsten and molybdenum high-speed steels have been formed. It is still widely used until now. The emergence of high-speed steel has caused a
revolution in cutting processing, greatly improving the productivity of metal cutting, and requiring a complete change in the structure of the machine tool to adapt to the cutting performance requirements of this new tool material. The emergence and further development of new machine tools, in turn, has led to the development of better tool materials, and tools have been stimulated and developed. Under the new manufacturing technology conditions, high-speed steel tools also have the problem of limiting the durability of the tool due to cutting heat when cutting at high speed. When the cutting speed reaches 700 °C, the high-speed steel
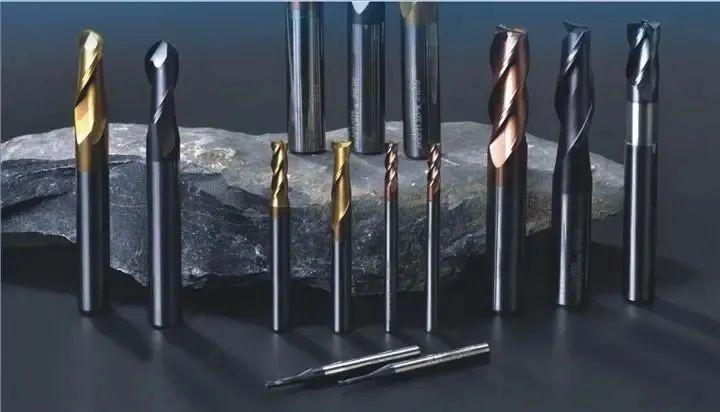
tip is completely dull, and at the cutting speed above this value, it is completely impossible to cut. As a result, carbide tool materials that maintain sufficient hardness under higher cutting temperature conditions than the above have emerged and can be cut at higher cutting temperatures.
Soft materials can be cut with hard materials, and in order to cut hard materials, it is necessary to use materials that are harder than it. The hardest substance on Earth at the moment is diamond. Although natural diamonds have long been discovered in nature, and they have a long history of using them as cutting tools, synthetic diamonds have also been successfully synthesized as early as the early 50s of the 20th century, but the real use of diamonds to widely make industrial cutting tool materials is still a matter of recent decades.
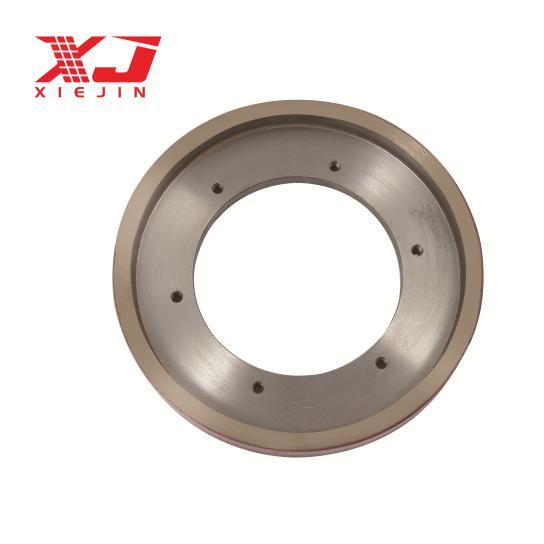
On the one hand, with the development of modern space technology and aerospace technology, the use of modern engineering materials is becoming more and more abundant, although the improved high-speed steel, cemented carbide, and new ceramic tool materials in the cutting of traditional processing workpieces, cutting speed and cutting productivity doubled or even dozens of times increased, but when using them to process the above materials, the durability of the tool and cutting efficiency is still very low, and the cutting quality is difficult to guarantee, sometimes even unable to process, the need to use sharper and more wear-resistant tool materials.
On the other hand, with the rapid development of modern machinery manufacturing and processing industry, the wide application of automatic machine tools, computer numerical control (CNC) machining centers, and unmanned machining workshops, in order to further improve processing accuracy, reduce tool change time, and improve processing efficiency, more and more urgent requirements are made to have more durable and stable tool materials. In this case, diamond tools have developed rapidly, and at the same time, the development of diamond tool materials has also been greatly promoted.
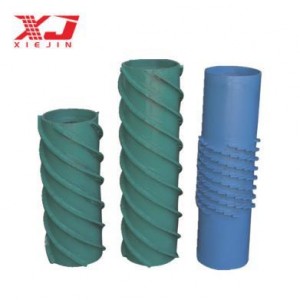
Diamond tool materials have a series of excellent properties, with high processing accuracy, fast cutting speed and long service life. For example, the use of Compax (polycrystalline diamond composite sheet) tools can ensure the processing of tens of thousands of silicon aluminum alloy piston ring parts and their tool tips are basically unchanged; Machining aircraft aluminum spars with Compax large-diameter milling cutters can reach cutting speeds of up to 3660m/min; These are incomparable to carbide tools.
Not only that, the use of diamond tool materials can also expand the processing field and change the traditional processing technology. In the past, mirror processing could only use the grinding and polishing process, but now not only natural single crystal diamond tools, but also in some cases can also be used PDC super-hard composite tools for super-precision close cutting, to achieve turning instead of grinding. With the application of super-hard tools, some new concepts have emerged in the field of machining, such as the use of PDC tools, the limiting turning speed is no longer the tool but the machine tool, and when the turning speed exceeds a certain speed, the workpiece and the tool do not heat. The implications of these groundbreaking concepts are profound and offer unlimited prospects for the modern machining industry.
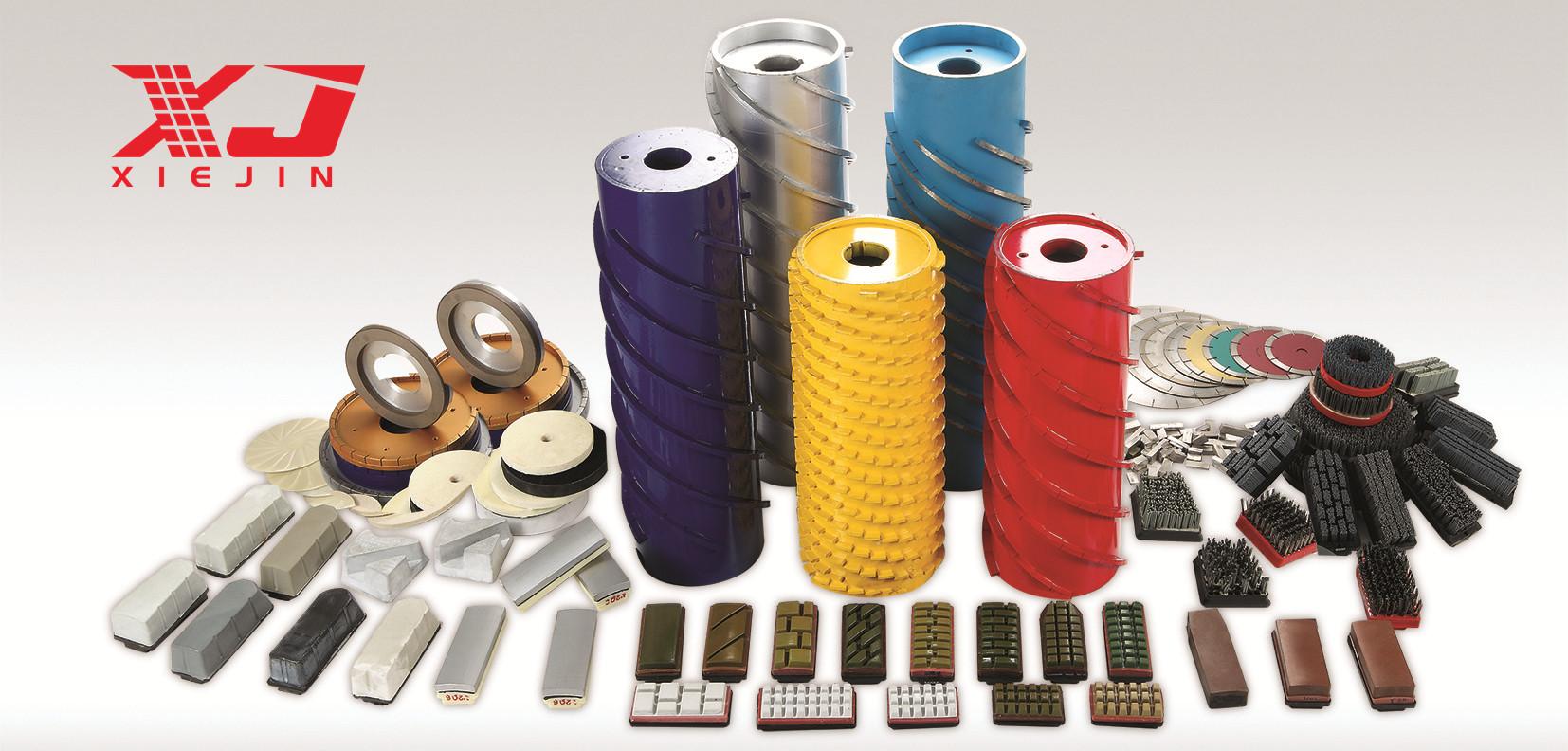
Post time: Nov-02-2022